От качества сварных швов напрямую зависит прочность, надежность и долговечность металлических конструкций, безопасность людей при эксплуатации соответствующих сооружений, оборудования, быстровозводимых зданий. Требования к швам перечислены в соответствующих стандартах и строительных нормативах и правилах. На производственных предприятиях обязательно проводят многоэтапный контроль качества, включая визуальный, неразрушающий ультрафиолетовый, радиографический.
Основные требования к сварным швам
Требования к сварным швам определены в ГОСТ 23118, а также соответствующими стандартами в зависимости от метода контроля качества и способа соединения металлических конструкций (вида сварки). Классификация сварных соединений металлоконструкций возможна по типу примыкания свариваемых деталей, виду шва, технологии сварки, толщины заготовок и металлов (сплавов), из которых они изготовлены.
Сварка стальных конструкций осуществляется в соответствии с разработанным и утвержденным технологическим процессом, оформляемым в виде типовых или технологических инструкций, руководящего документа (например, РД-34.15.132-96), проекта производства сварочных работ (ППСР), разрабатываемого конкретным предприятием.
К общим требованиям к сварным швам металлоконструкций относится следующее:
- Механические свойства определяют по ГОСТ 6996. В результате испытаний временное сопротивление разрыву стали должно быть не ниже соответствующего сопротивления основного металла. Твердость металла шва, зоны термического влияния в металлоконструкциях 1-й группы – до 350 HV, остальных групп – до 400 HV. В зоне термического влияния ударная вязкость – от 24 Дж/см2.
- Отклонения от требуемых размеров швов должны соответствовать допустимым значениям по ГОСТ 8713, 14771, 11533, 5264 и др.
- После завершения сварки швы зачищают от шлака, брызг, натеков. Если проводится оценка качества и соответствия требованиям швов уже введенных в эксплуатацию конструкций, то требуется очистка от краски, ржавчины, загрязнений. Проверка качества сварных швов методами неразрушающего контроля проводится до покраски, нанесения антикоррозийного покрытия.
- Вблизи шва проставляется личное клеймо сварщика, выполнившего данный шов. Если сварка всей металлоконструкции (сборочного элемента) выполняется одним сварщиком, то клеймо можно ставить рядом с маркировкой марки.
Методы контроля качества сварных швов
Выделяют следующие способы контроля качества соединений:
- Визуальный. Цель – выявление дефектов, недопустимых для приемки и/или дальнейшей эксплуатации конструкции (трещины, расслоения, закаты, вмятины, раковины, рванины, шлаковые включении и пр.). Проводится специалистом без использования каких-либо инструментов и приборов.
- Измерительный. Цель – проверка геометрических размеров, а также оценка размеров поверхностных дефектов, выявленных в ходе инструментального контроля. Для проведения измерительного контроля применяются шаблоны (универсальный, специальный), линейка, щуп, штангенциркуль, контрольный стенд.
- Радиационный. Технологически представляет собой рентгенографическое исследование швов на предмет не выявленных при визуальном и измерительном контроле внешних, внутренних дефектов и дефектов формы соединения. Различают радиографический, радиоскопический, радиометрический методы.
- Акустический. Метод неразрушающего контроля, основанный на способности ультразвука проникать вглубь металла для определения как внутренних, так и поверхностных дефектов.
- Капиллярный. Способ проверки сварных соединений на наличие дефектов, выходящих на поверхность. С помощью специальных проникающих жидкостей (пенетрантов), способных проникать внутрь шва даже через невидимые невооруженным глазом микротрещины и поры. Различают 3 метода капиллярного контроля в зависимости от свойств используемых жидкостей: цветной, люминесцентный, люминесцентно-цветной.
- Магнитный. Метод контроля, используемый для выявления поверхностных, подповерхностных несплошностей. В зависимости от технологии различают магнито-феррозондовый, магнито-порошковый, магнито-графический. При магнито-графическом методе также возможна проверка швов на внутренние несплошности.
- Течеискание. Способы проверки герметичности сварных соединений для выявления сквозных дефектов замкнутых конструкций, труб, в которых транспортировка рабочих сред осуществляется под высоким давлением. Может осуществляться радиационным, масс-спектрометрическим, манометрическим, галоидным, химическим, газоаналитическим, пузырьковым и другими методами.
Конкретная технология проверки сварных швов на соответствие требованиям должна указываться в нормативно-технической документации на контроль.
Основным методом проверки сварных соединений металлических конструкций на соответствие требованиям при приемке является визуальный. Проводится ОТК заказчика на месте монтажа металлоконструкций. Оценка качества швов методом визуального контроля проводится в условиях достаточной освещенности контролируемых поверхностей – минимальное значение составляет 500 Лк.
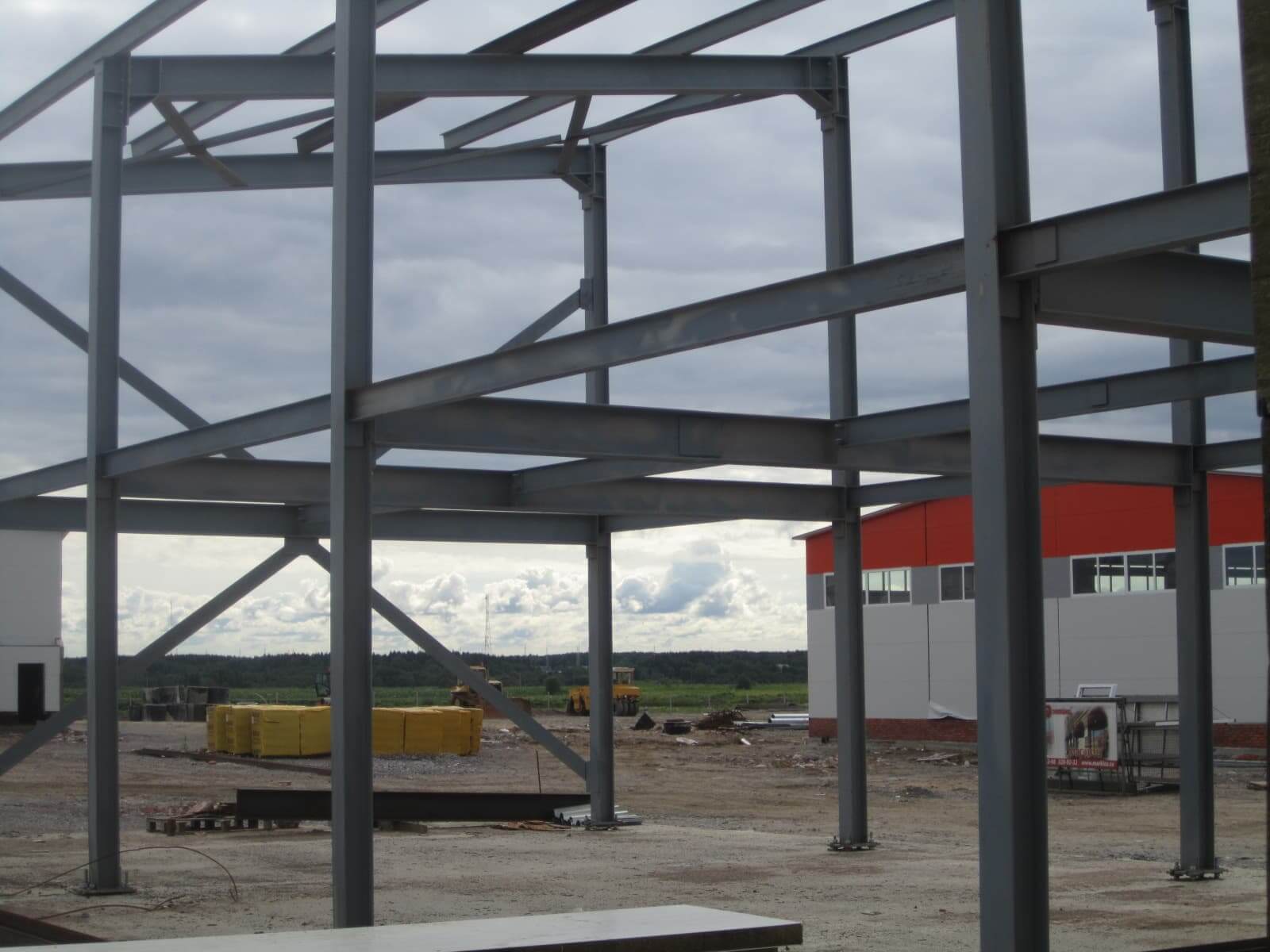
При визуальном контроле сварные соединения металлических конструкций должны удовлетворять следующим требованиям:
- Поверхность – гладкая или чешуйчатая.
- Плавный переход от шва к основному металлу.
- Отсутствие трещин сварного шва и околошовной зоны.
Остальные способы проверки качества сварных соединений конструкций различного назначения применяются на заводе-изготовителе, а также при ремонте, эксплуатации, проведении обследований состояния металлоконструкций с целью установления срока службы, необходимости текущего ремонта при выявлении критических дефектов, деформаций.